Unlocking Success in Manufacturing with a Premier Plastic Molding Factory
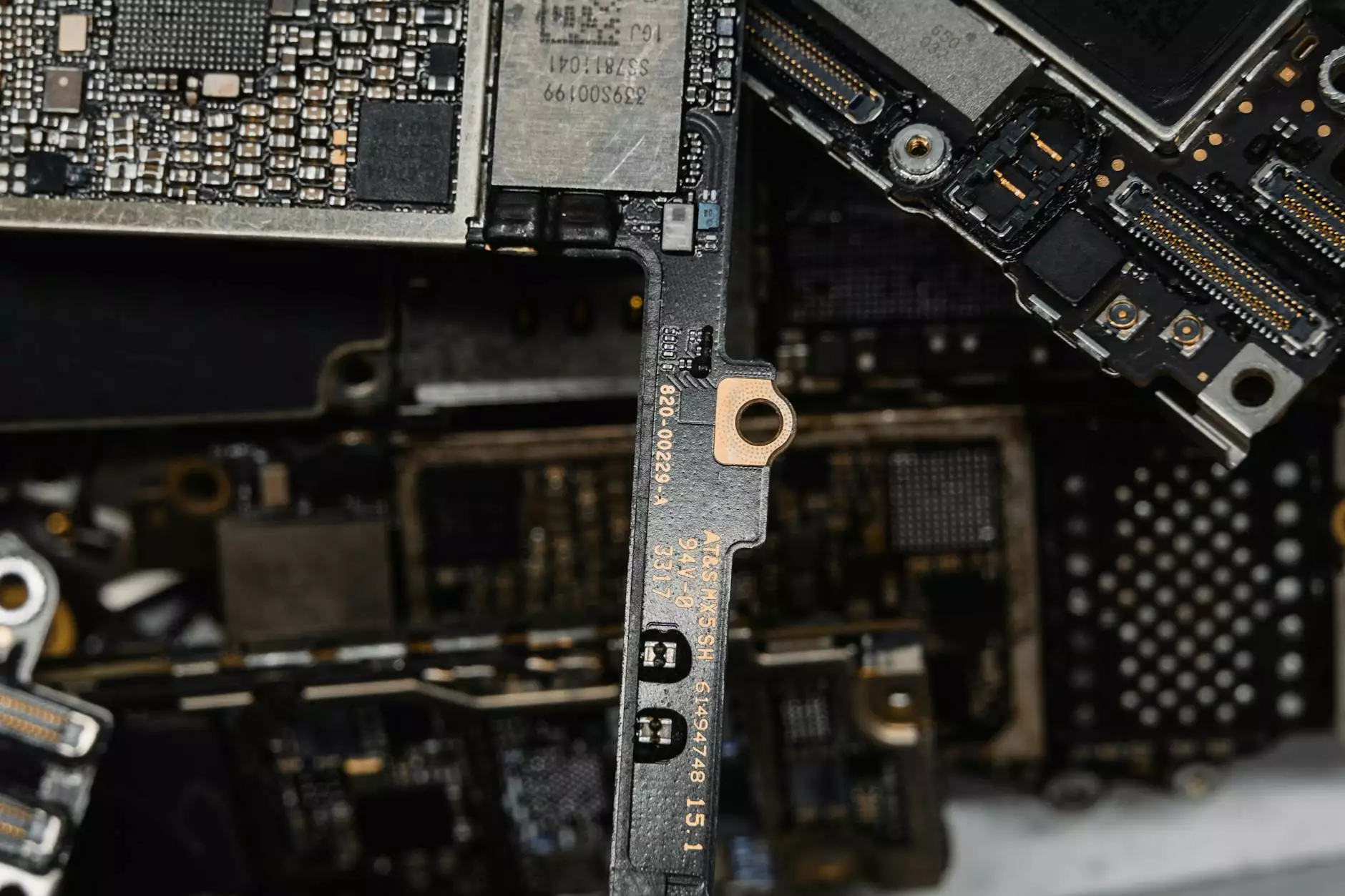
In today's rapidly evolving industrial landscape, precision, efficiency, and innovation are the cornerstones of successful manufacturing. Among the pivotal components that drive the manufacturing sector forward, a plastic molding factory stands out as an essential entity, responsible for transforming raw plastics into intricate, high-quality components used across myriad industries. This article delves deep into the strategic advantages, technological excellence, and industry leadership of a plastic molding factory, specifically through the lens of a top-tier enterprise like Deep Mould, renowned among metal fabricators and manufacturing professionals worldwide.
Why a Plastic Molding Factory Is a Pillar of Modern Manufacturing
Manufacturing has undergone a paradigm shift over the past decades, primarily driven by advancements in plastics processing technology. A syntheses of craftsmanship and cutting-edge machinery, a plastic molding factory offers tangible benefits including:
- Cost Efficiency: Streamlined production processes reduce overall manufacturing costs, enabling competitive pricing.
- High Precision and Tolerance: Advanced molding techniques allow for the creation of complex and detailed parts with strict tolerances.
- Material Versatility: Wide range of plastics from thermoplastics to thermosets, suitable for diverse applications.
- Mass Production Capabilities: High-volume manufacturing that maintains consistent quality across thousands or millions of parts.
- Design Flexibility: Rapid prototyping and customized solutions facilitate innovative product development.
Technological Innovations Powering Leading Plastic Molding Factory Operations
In the competitive world of plastics manufacturing, staying at the forefront of technology is imperative. Progressive plastic molding factories incorporate a blend of advanced machinery, automation, and integrated quality control systems:
Injection Molding Precision
This dominant process involves injecting molten plastic into custom-designed molds, allowing for rapid production of complex geometries. High-precision injection molding machines now operate with multi-cavity molds, hot runner systems, and servo-driven controls to enhance efficiency and reduce cycle times.
Rapid Prototyping and 3D Mold Design
Using computer-aided design (CAD) and computer-aided manufacturing (CAM) software, a plastic molding factory can produce prototypes swiftly, allowing for fast iteration and optimization before committing to mass production molds.
Automation and Quality Assurance
Robotic arms, automated material handling, and real-time monitoring systems enable factories like Deep Mould to maintain consistent quality, minimize human error, and increase throughput.
Quality Control and Certification Standards in a Leading Plastic Molding Factory
Achieving industry excellence requires adherence to rigorous quality standards. Leading plastic molding factories implement comprehensive quality management systems, including:
- ISO 9001 Certification — Ensures consistent quality across all production processes.
- ISO 13485 or IATF 16949 — For specialized industries such as medical devices or automotive components.
- Material Testing and Inspection — Utilization of advanced equipment like coordinate measuring machines (CMM), tensile testers, and spectrometers.
- In-Process Quality Checks — Continuous monitoring during molding to preempt defects and ensure precision.
The Strategic Advantages of Partnering with a Plastic Molding Factory like Deep Mould
Choosing the right plastic molding factory can significantly impact a company's success trajectory. Deep Mould, with its extensive experience as a top-tier metal fabricator and plastics manufacturer, offers unparalleled advantages:
- End-to-End Solutions — From product conceptualization and mold design to production and finishing, providing clients with comprehensive support.
- Customization and Flexibility — Capable of managing small-batch runs to large-scale production, ensuring project-specific needs are met.
- Material Expertise — Extensive knowledge of plastics and metals, enabling optimal material selection for durability, aesthetics, and cost-effectiveness.
- Innovative Manufacturing Techniques — Integration of latest molding methods like micro-injection molding, insert molding, and overmolding.
- Global Reach and Short Lead Times — International logistics and efficient production schedules guarantee rapid delivery.
Industries Transformed by Advanced Plastic Molding Factory Manufacturing
The versatility of a reliable plastic molding factory extends across numerous sectors, such as:
Automotive Industry
Production of lightweight, durable interior parts, exterior trim, and electrical components that enhance vehicle efficiency and aesthetics.
Medical Devices and Healthcare
Fabrication of sterile, high-precision components such as syringes, diagnostic equipment housings, and implantable devices using biocompatible plastics.
Electronics and Consumer Goods
Manufacturing of small, complex plastic parts like connectors, cases, and buttons with a focus on durability and aesthetic appeal.
Packaging and Consumer Products
Designing innovative packaging solutions that combine functionality with attractive appearance, utilizing eco-friendly plastics.
Industrial Machinery and Tools
Creating robust and wear-resistant plastic components that withstand heavy-duty operational environments.
The Future of Plastic Molding: Innovation and Sustainability
As industries evolve, so do the demands on plastic molding factories. The future emphasizes not only innovation in design and technology but also a strong commitment to sustainability:
- Biodegradable and Recycled Materials — Incorporating eco-friendly plastics to reduce environmental impact.
- Energy-Efficient Processes — Leveraging low-energy machinery and process optimization to minimize carbon footprint.
- Smart Manufacturing — Incorporating Industry 4.0 technologies such as IoT sensors, real-time data analytics, and automation for smarter quality control and logistics.
- Design for Sustainability — Creating products that are easier to recycle and have a longer lifecycle.
Why Deep Mould Exemplifies Excellence in Plastic Molding Factory Operations
Deep Mould epitomizes industry leadership by continuously integrating innovation, quality, and customer-centric services. With decades of experience in metal fabricators and plastics manufacturing, the company offers:
- Advanced Molding Equipment — Access to high-precision injection molding machines capable of handling complex articles.
- Innovative Mold Design — Utilizing 3D CAD/CAM systems for optimized mold construction.
- Quality-Focused Culture — Strong quality management systems align with international standards.
- Sustainability Initiatives — Commitment to environmentally responsible manufacturing practices.
- Global Customer Support — Dedicated teams providing technical assistance, quick turnaround, and flexible solutions.
Conclusion: Elevate Your Manufacturing Success with a Premier Plastic Molding Factory
Whether you are seeking to develop innovative products, scale production efficiently, or adhere to strict quality standards, partnering with a plastic molding factory like Deep Mould can elevate your manufacturing capabilities. The combined strengths of technological innovation, quality assurance, and industry expertise make such factories indispensable to the modern manufacturing ecosystem. By emphasizing precision, cost-effectiveness, and sustainability, leading plastic molding factories are shaping the future of industries worldwide.
Unlock your company's potential by choosing a trusted partner committed to excellence in plastic molding and metal fabrication. Explore the extensive offerings and industry leadership of Deep Mould today and propel your manufacturing projects to new heights.