Understanding Precision CNC Machining Factories
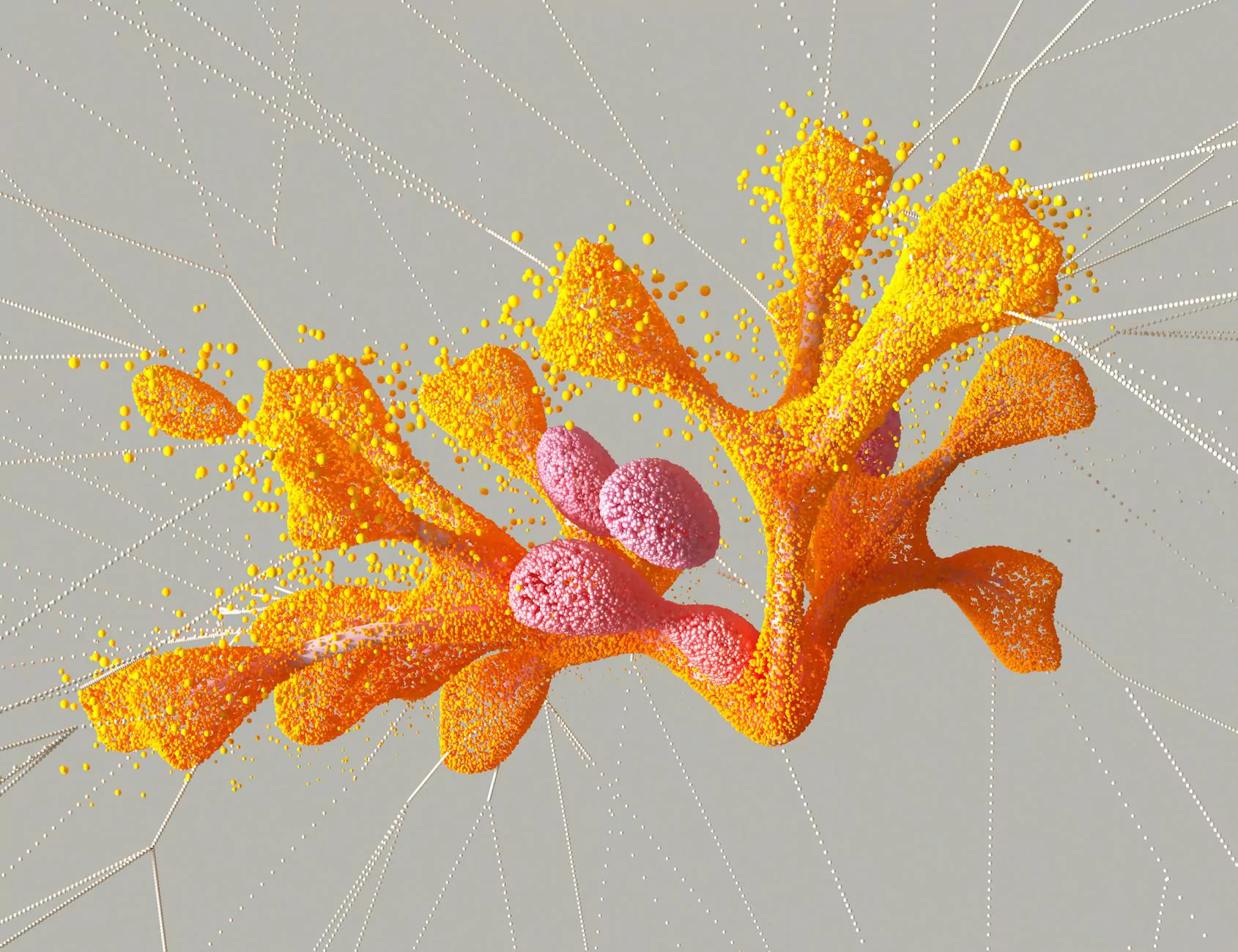
The realm of precision CNC machining factories is a fascinating intersection of technology and craftsmanship. In today's fast-paced industrial environment, the demand for high-quality, precise metal parts has surged, making these factories essential for manufacturers across various industries. This article delves deep into the intricacies of precision CNC machining, emphasizing its importance, processes, and the advantages it brings to metal fabricators.
The Basics of CNC Machining
CNC stands for Computer Numerical Control, which refers to the automation of machine tools through computers executing pre-programmed sequences of machine control commands. The CNC machining process involves cutting, shaping, and manipulating materials to create precise components needed in manufacturing.
How CNC Machining Works
The process begins with a CAD model (Computer-Aided Design) that outlines the specifications of the desired part. This model is then translated into a CNC program, which instructs the machine on how to move and operate. The following steps outline the general CNC machining workflow:
- Design Creation: Engineers create a detailed design using CAD software.
- Programming: The CAD design is converted into a CNC program using CAM software (Computer-Aided Manufacturing).
- Setup: The CNC machine is set up with the appropriate tools and the material is secured in place.
- Machining: The CNC machine executes the program, cutting and shaping the material as specified.
- Finishing: The part is polished or treated to meet the desired finish and tolerance levels.
Types of CNC Machining Processes
Precision CNC machining encompasses several processes, each suitable for different applications:
- Milling: Uses rotating cutting tools to remove material from a workpiece, ideal for complex shapes.
- Turning: Involves rotating the workpiece while a stationary cutting tool shapes it, commonly used for cylindrical parts.
- EDM (Electrical Discharge Machining): Removes material through electrical discharges, useful for intricate designs.
- 3D Printing: Additive manufacturing that builds parts layer by layer, increasingly integrated with CNC processes.
Advantages of Precision CNC Machining
Utilizing precision CNC machining factories offers numerous advantages for metal fabricators, including:
- High Precision: CNC machining achieves tolerances as tight as 0.001 inches, ensuring quality and reliability.
- Efficiency: Automation speeds up production times and reduces manpower costs, enhancing overall productivity.
- Versatility: Capable of working with various materials, including metals, plastics, and composites.
- Complex Geometries: CNC technology can create intricate designs that are difficult or impossible to achieve manually.
- Reproducibility: Once programmed, CNC machines can produce identical parts consistently, ensuring uniformity in production.
The Role of Precision CNC Machining Factories in Modern Manufacturing
In the current landscape of metal fabricators, precision CNC machining factories play a pivotal role. They are critical to numerous industries such as:
- Aerospace: Produces lightweight yet strong components for aircraft and spacecraft.
- Automotive: Manufactures engine parts, chassis, and various other components essential for vehicle assembly.
- Medical: Develops precise components used in medical devices, surgical instruments, and implants.
- Electronics: Creates intricate parts for devices, ensuring they meet stringent design requirements.
Continuous Improvement in CNC Machining Technology
The field of precision CNC machining is characterized by continuous innovation. New technologies and methodologies are playing a significant role in enhancing machining capabilities. Some of these advancements include:
- Advanced Software: Modern CAM software allows for more efficient programming and simulation, reducing setup times and waste.
- Automation and Robotics: The integration of robotics in machining processes further increases efficiency and consistency.
- Smart Manufacturing: Technologies such as IoT (Internet of Things) are being utilized for real-time monitoring and predictive maintenance of machinery.
- Eco-Friendly Practices: Increased focus on sustainability has led to practices that minimize waste and energy consumption in machining processes.
Key Considerations When Choosing a Precision CNC Machining Factory
If you are a metal fabricator or a business in need of precision parts, selecting the right CNC machining factory is crucial. Here are some vital factors to consider:
- Capabilities: Ensure the factory specializes in the required machining processes and has experience with your specific materials.
- Technology: Look for factories equipped with the latest CNC machines and software for optimal performance.
- Quality Control: Inquire about their quality assurance processes, including certifications such as ISO 9001.
- Turnaround Time: Assess their production schedules to meet your deadlines without compromising quality.
- Customer Support: A responsive and knowledgeable support team is essential for addressing any concerns throughout your project.
Conclusion
In summary, precision CNC machining factories are indispensable in today's manufacturing landscape, providing unmatched efficiency, accuracy, and versatility. As industries continue to evolve, these factories will remain at the forefront of innovation, driving advancements that cater to the complex demands of modern engineering. By understanding the processes involved and choosing the right factory, businesses can achieve superior outcomes and maintain a competitive edge in their respective fields.
Explore More with DeepMould.net
To learn more about our services as a leading provider in the metal fabrication industry, visit DeepMould.net. Discover how our precision CNC machining capabilities can elevate your manufacturing processes, ensuring precision and excellence in every part we produce.