The Advantages of Remote Liftstation Systems in Business
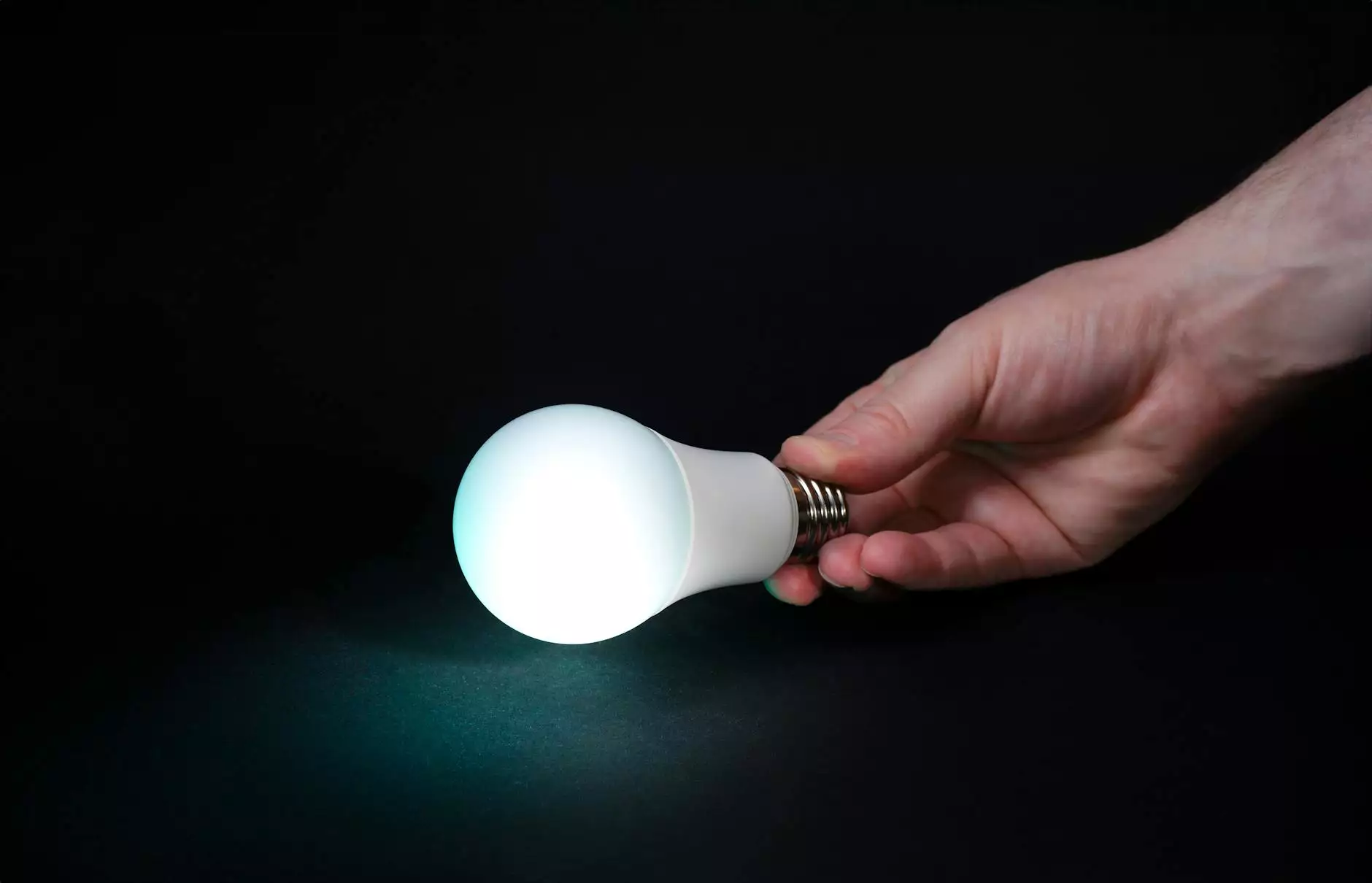
In today's rapidly evolving industrial landscape, businesses are increasingly relying on advanced technologies to streamline their operations, enhance safety, and improve overall efficiency. One such innovation that has gained traction in recent years is the remote liftstation system. This technology not only optimizes workflow but also ensures that safety equipment functions seamlessly. In this article, we will delve deep into the significance of remote liftstation systems, particularly within the Auto Parts & Supplies and Safety Equipment sectors.
Understanding Remote Liftstation Systems
A remote liftstation is a system that allows for the management and monitoring of lifting equipment from a distance. This includes various devices and machinery used for transporting goods in warehouses, construction sites, and manufacturing plants. The primary goal of implementing such systems is to enhance safety and operational productivity by providing real-time data about equipment status, location, and performance.
Key Features of Remote Liftstation Systems
- Real-Time Monitoring: Remote liftstations provide real-time insights into equipment performance, allowing businesses to respond promptly to any issues that may arise.
- Data Analytics: The data collected through these systems can be analyzed to improve future operations and maintenance schedules.
- Remote Control: Operators can manage equipment remotely, reducing the need for on-site personnel and minimizing human error.
- Improved Safety: By monitoring equipment from a distance, businesses can identify potential hazards before they escalate into major incidents.
The Business Benefits of Implementing Remote Liftstation Systems
1. Enhanced Operational Efficiency
One of the most significant advantages of incorporating a remote liftstation in your operations is the enhanced efficiency it brings. By having control and monitoring capabilities from a remote location, businesses can:
- Optimize workflow by ensuring that lifting equipment is available when needed.
- Reduce downtime due to quicker identification of equipment failures.
- Improve productivity through better allocation of resources.
2. Cost Savings
Implementing a remote liftstation can lead to substantial cost savings over time. This includes:
- Lower Labor Costs: Reducing the need for constant on-site personnel can result in decreased labor expenses.
- Decreased Maintenance Costs: Predictive maintenance enabled by real-time data helps prevent costly repairs and extends the lifespan of equipment.
- Energy Efficiency: Remote liftstations can optimize power usage, leading to lower energy bills.
3. Improved Safety Standards
The safety of employees and equipment is paramount in any industrial setting. Remote liftstations contribute significantly to safety by:
- Providing alerts and notifications regarding equipment malfunctions or safety violations.
- Allowing for remote operation, reducing the need for personnel in dangerous areas.
- Facilitating regular safety audits and compliance checks through data tracking.
Case Studies: Success Stories of Remote Liftstation Implementation
To illustrate the impact of remote liftstation systems, let's take a look at a few success stories from the Auto Parts & Supplies and Safety Equipment sectors.
Case Study 1: Auto Parts Supply Company
A leading auto parts supplier integrated remote liftstations to manage their warehouse operations. The result was:
- A 30% increase in operational efficiency.
- Reduction in equipment downtime from 20% to 5%.
- Improved employee safety ratings, with a significant drop in on-site accidents.
Case Study 2: Safety Equipment Manufacturer
In another instance, a safety equipment manufacturer adopted remote liftstations to streamline their production lines. Their outcomes included:
- Enhanced monitoring capabilities that reduced equipment failures by 40%.
- Cost savings of up to 25% through reduced maintenance and labor costs.
- Improved compliance with safety regulations, leading to fewer fines and violations.
Challenges and Considerations When Implementing Remote Liftstations
Despite the numerous benefits, transitioning to a remote liftstation system is not without its challenges. Businesses should consider the following:
- Initial Investment: The upfront investment can be significant, but it’s essential to view this as a long-term savings strategy.
- Training Requirements: Employees will need training to effectively utilize remote systems, which requires time and resources.
- Data Security: With increased connectivity comes the risk of cyber vulnerabilities; thus, robust security measures need to be implemented.
The Future of Remote Liftstation Systems
The landscape of industrial operations is continually evolving. As technology advances, we can expect remote liftstation systems to become increasingly sophisticated. The integration of IoT (Internet of Things), machine learning, and artificial intelligence will allow for even more enhanced performance, predictive maintenance, and data analytics capabilities.
Conclusion
As businesses in the Auto Parts & Supplies and Safety Equipment sectors strive to improve efficiency, safety, and profitability, remote liftstation systems will undoubtedly play a pivotal role. By embracing this advanced technology, companies can secure a competitive edge and foster a culture of safety and efficiency.
Investing in a remote liftstation system is not merely a technological upgrade; it is a strategic move towards building a smarter and safer workplace for all. As we move toward a more interconnected industrial future, those who adapt and innovate will reap the rewards.