The Transformative Power of Polycarbonate in 3D Printing
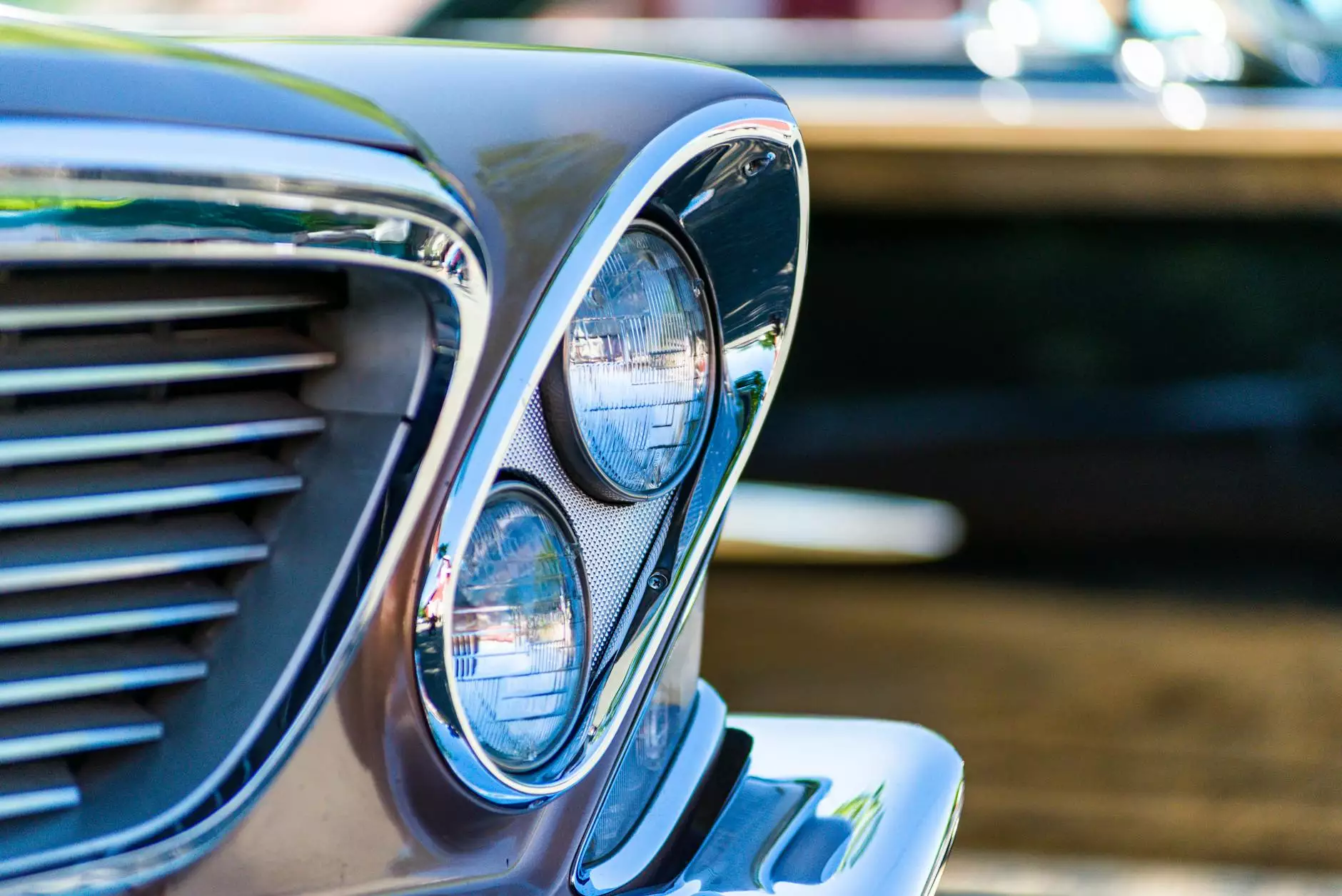
Polycarbonate has emerged as a revolutionary material in the realm of 3D printing, transforming how businesses approach prototyping and product development. This thermoplastic is valued not only for its durability but also for its exceptional versatility, making it an ideal choice for a wide range of applications. In this extensive article, we will delve into the properties, benefits, applications, and future of polycarbonate in the 3D printing industry.
Understanding Polycarbonate: A Comprehensive Overview
Before diving into its applications, it's essential to understand what polycarbonate is. This material is a type of thermoplastic that contains carbonate groups in its chemical structure. Notably, it is renowned for several remarkable properties, including:
- High Impact Resistance: Polycarbonate is incredibly strong, able to withstand significant impact without breaking or deforming.
- Transparency: It can be manufactured in clear forms allowing it to serve as a glass alternative in various applications.
- Temperature Resistance: Polycarbonate retains its properties over a wide range of temperatures, making it suitable for different environments.
- Lightweight: This material is considerably lighter compared to traditional materials like glass or metal.
- UV Resistance: When treated, polycarbonate can resist ultraviolet light, preventing degradation over time.
Why Polycarbonate is a Preferred Material in 3D Printing
In recent years, 3D printing has revolutionized manufacturing processes, enabling businesses to produce complex geometries that were once challenging or impossible to achieve. The use of polycarbonate in 3D printing comes with a plethora of advantages:
1. Durability and Longevity
Unlike other common 3D printing materials such as PLA or ABS, polycarbonate boasts superior durability. This makes it suitable for end-use products that must endure wear and tear. Its resilience allows for the production of parts that require strength, such as brackets, fittings, and housings.
2. Excellent Thermal Stability
One of the standout features of polycarbonate is its ability to maintain structural integrity at high temperatures. Unlike some plastics that can warp in heat, components printed with polycarbonate can withstand temperatures up to 120°C (248°F), making it ideal for automotive and aerospace applications.
3. Design Flexibility
The adaptability of polycarbonate in 3D printing allows designers and engineers to experiment freely with their projects. Complex shapes, hollow structures, and intricate detail can be easily achieved, empowering innovation.
4. Cost-Effectiveness
While the initial cost of polycarbonate filament may be higher than that of other materials, the long-term savings from reduced replacement costs and decreased production time make it a cost-effective option for many businesses.
5. High Surface Finish Quality
Parts printed with polycarbonate tend to have a smooth surface finish, reducing the need for post-processing. This is particularly beneficial in industries where aesthetics are paramount, such as consumer electronics and automotive trim.
Applications of Polycarbonate in Various Industries
The unique properties of polycarbonate have led to its adoption across numerous industries. Here are some prominent applications:
1. Aerospace and Automotive
In the aerospace and automotive sectors, weight is a critical concern. Polycarbonate is used for producing various components, such as dashboard displays, light covers, and even structural elements, helping to reduce overall vehicle weight while maintaining strength.
2. Electronics
Many electronic devices utilize polycarbonate for housings, connectors, and insulators due to its excellent electrical insulation properties and thermal stability. The material's clarity also makes it ideal for protective covers over screens and displays.
3. Medical Devices
The medical industry benefits from the use of polycarbonate due to its biocompatibility and ability to be sterilized. Items like surgical instruments, housings for diagnostic equipment, and drug delivery devices are frequently 3D printed using polycarbonate.
4. Consumer Goods
Many consumer products, from household appliances to sporting goods, incorporate polycarbonate due to its lightweight and durability. It allows for innovative designs while ensuring the products can withstand rigorous daily use.
5. Architectural Applications
In construction and architecture, polycarbonate can be used in skylights, safety glazing, and indoor partitions, offering an aesthetically pleasing and functional option that enhances natural light and energy efficiency.
Challenges of Using Polycarbonate in 3D Printing
While polycarbonate is celebrated for its many benefits, it's not without challenges in the 3D printing process:
- Printing Difficulty: Polycarbonate can be difficult to print due to its tendency to warp or shrink as it cools, requiring a well-calibrated printer and optimal temperature settings.
- Equipment Requirements: To print with polycarbonate, a printer with a high-temperature nozzle and a heated bed is necessary, which may not be available on all 3D printers.
- Material Costs: The cost of polycarbonate filament is generally higher than cheaper alternatives like PLA, which may deter some hobbyists and small businesses.
Future Trends in Polycarbonate 3D Printing
The future of polycarbonate in 3D printing looks promising, with ongoing research and development leading to innovative methodologies and applications:
1. Enhanced Printing Techniques
As 3D printing technology continues to advance, improved printing techniques will likely emerge to address challenges with polycarbonate. This includes better filament formulations and optimized slicers that can reduce warping and improve layer adhesion.
2. Biodegradable Polycarbonate
As sustainability becomes increasingly important, innovations such as biodegradable versions of polycarbonate may enter the market, combining the advantages of this material with eco-friendliness.
3. Integration with Other Materials
Hybrid printing, which combines polycarbonate with other materials to create multi-functional parts, is anticipated to gain popularity. This will allow manufacturers to take advantage of the properties of different materials in a single print.
4. Customization and Personalization
With advancements in digital technology, the use of polycarbonate in customizable 3D printed products will likely expand, allowing businesses to respond to consumer demands for personalized goods effectively.
Conclusion
In conclusion, polycarbonate is a remarkable material that is not only expanding the horizons of 3D printing but also enhancing the capabilities of various industries. Its unique combination of strength, flexibility, and durability makes it a preferred choice for businesses looking to innovate and improve their production processes. By embracing polycarbonate in 3D printing, companies can unlock new opportunities for design and functionality, reinforcing their competitive advantage in a rapidly evolving market.
As we continue to explore the potential of polycarbonate in 3D printing, it is evident that this material will play a vital role in shaping the future of manufacturing and product design. Whether you're in aerospace, medical, automotive, or consumer goods, integrating polycarbonate into your 3D printing strategy could be the key to unlocking unprecedented levels of efficiency and innovation.